Le Victoire du Concours de Machines (Paris-Brest-Paris)
Une fois de plus, l'équipe Victoire a pris la décision de s'engager pour le Concours De Machines 2019. Cette année, le règlement était écrit par le magazine 200, sous la forme d'une lettre d'un certain Mr Rêveur décrivant les fantasmes d'un habitué de longue distance parti à la recherche d'une nouvelle monture. Voici donc notre proposition, respectant les souhaits de Mr Rêveur, arrivée en tête du Concours de Machines 2019.
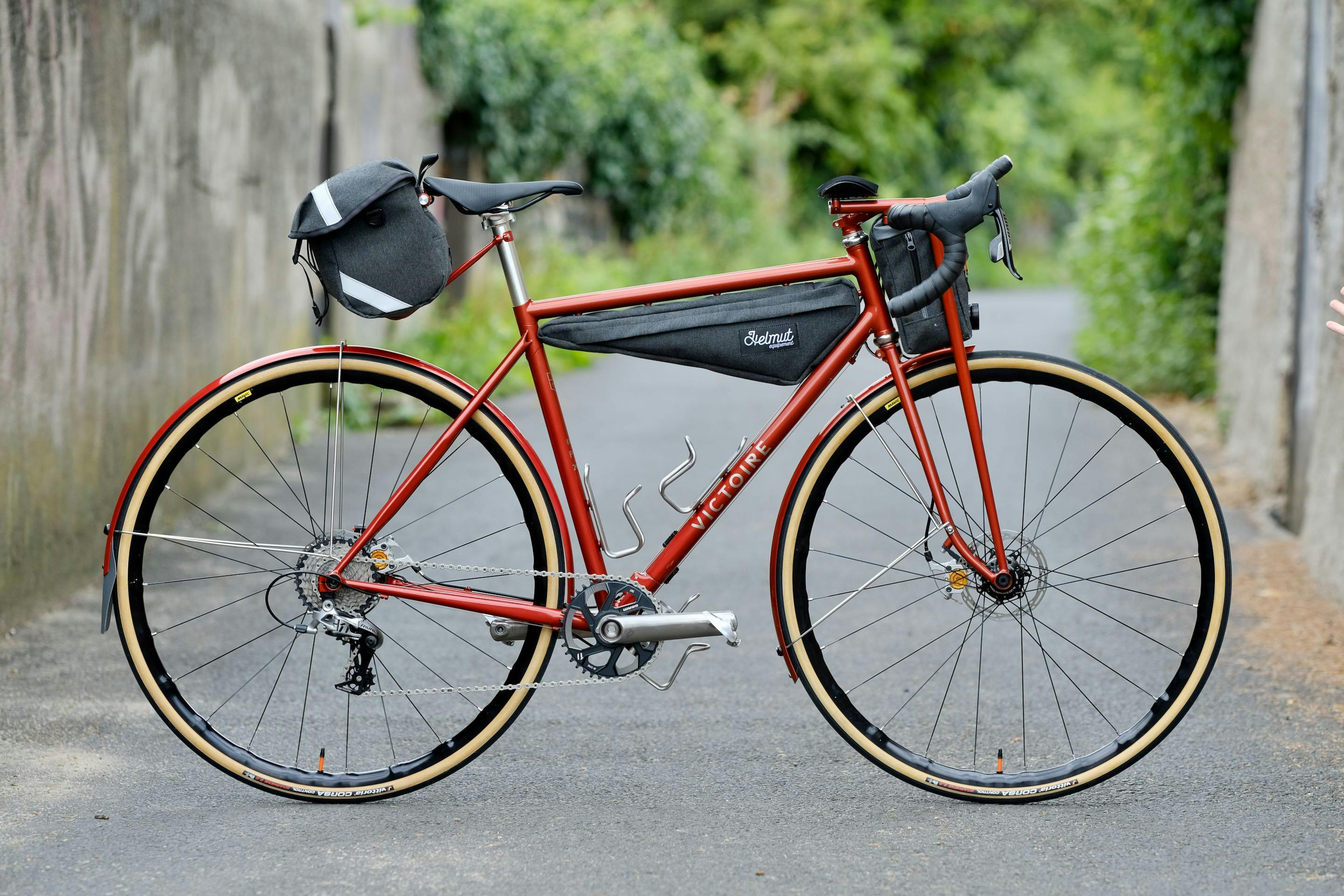
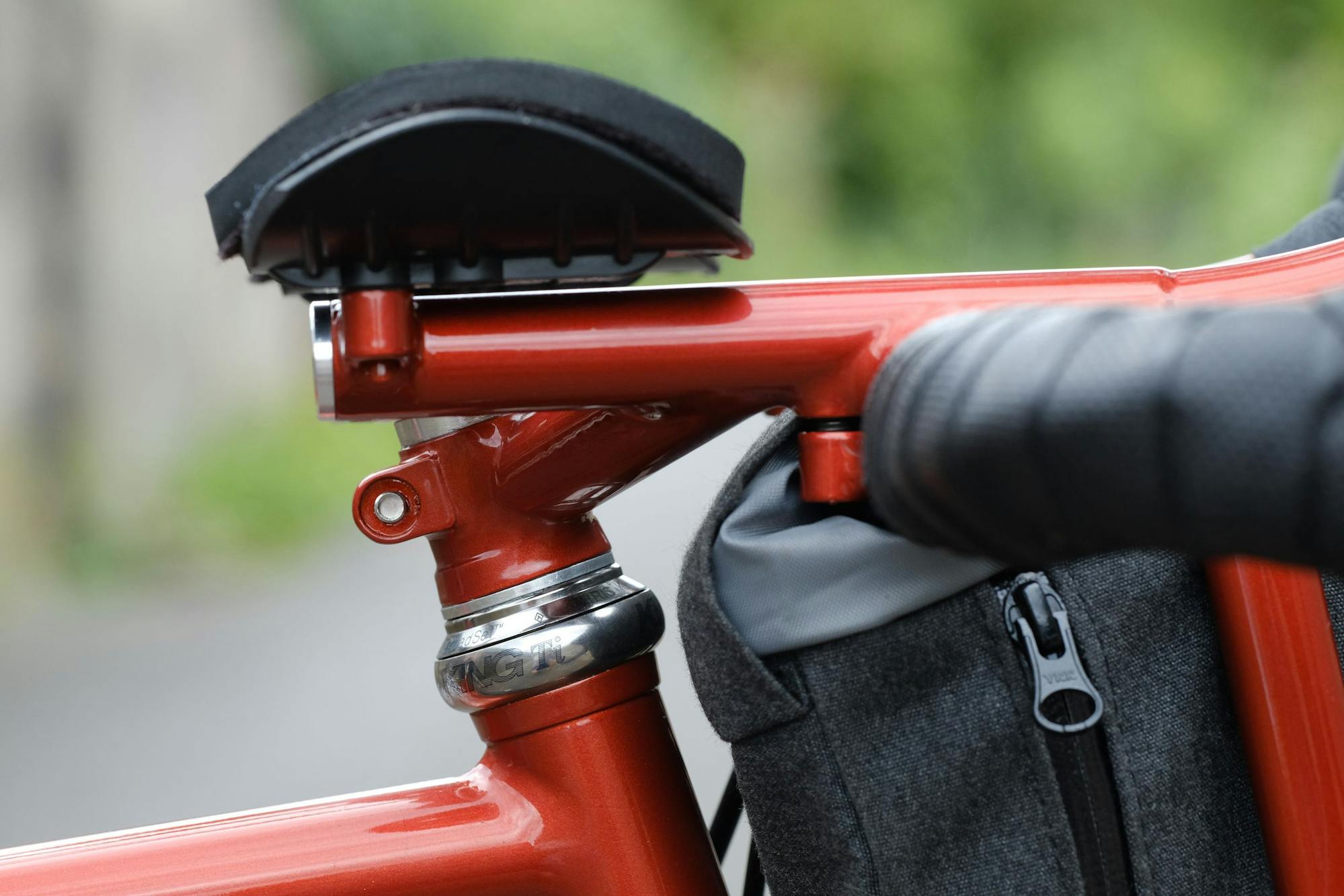
Autour de la table dès le mois de février, plusieurs choses nous sont apparues évidentes : ce vélo pour le Concours ne serait pas seulement un modèle permettant de montrer notre savoir-faire, ce serait aussi un terrain d’exploration, un prototype nous permettant de sortir de notre zone de confort et de tester de nouvelles idées et enfin un vélo que nous garderons dans notre showroom, comme les modèles créés pour les éditions précédentes.
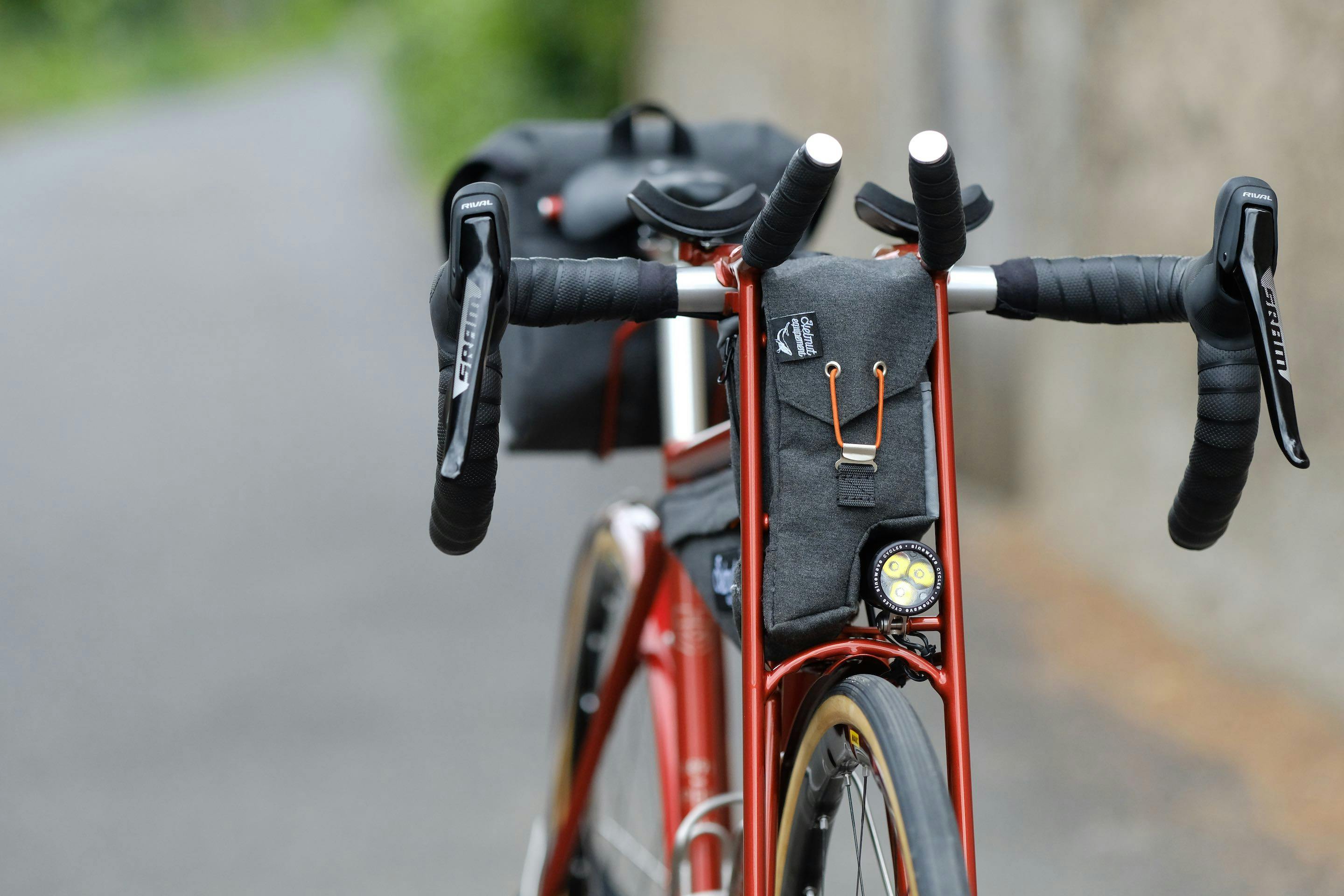
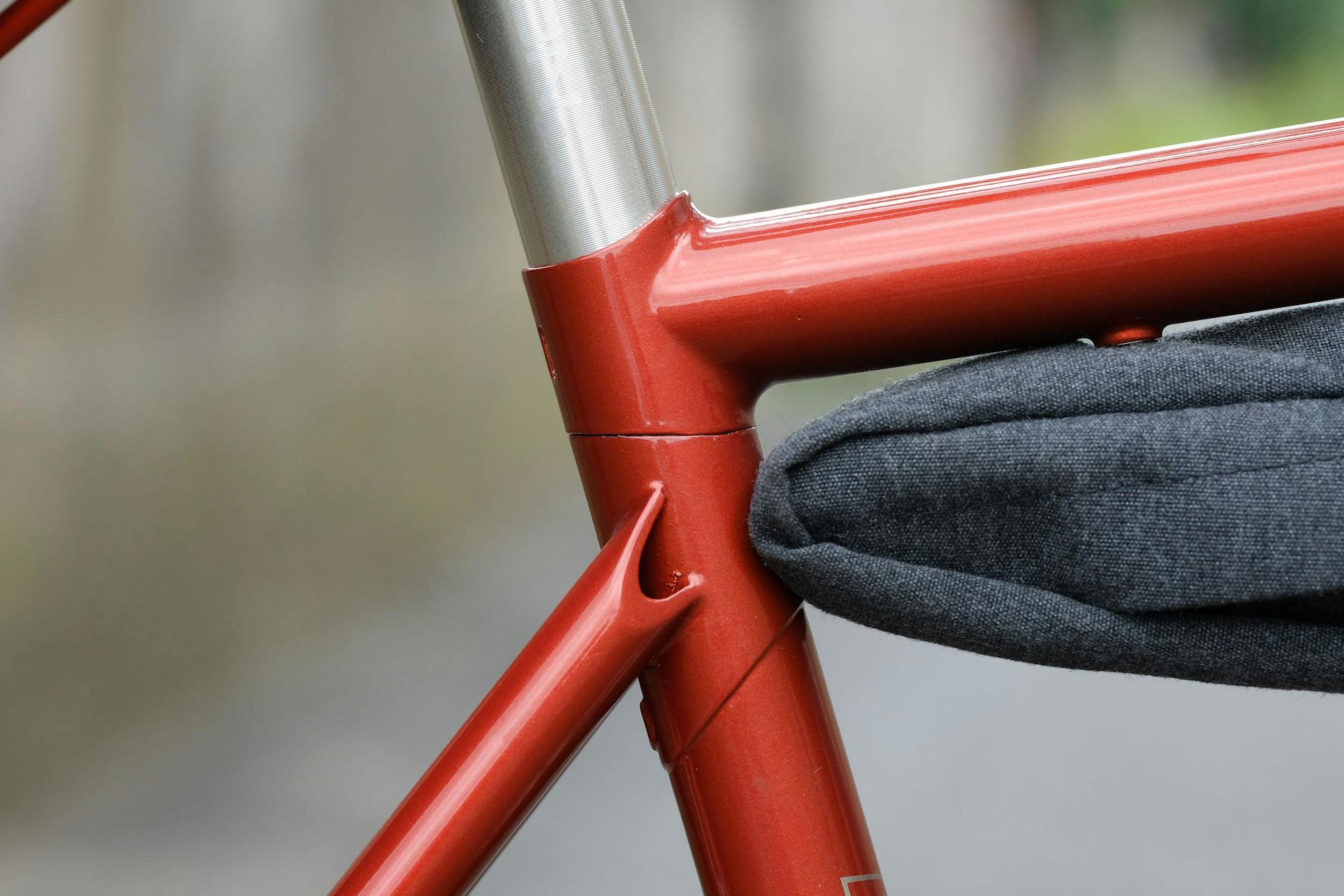
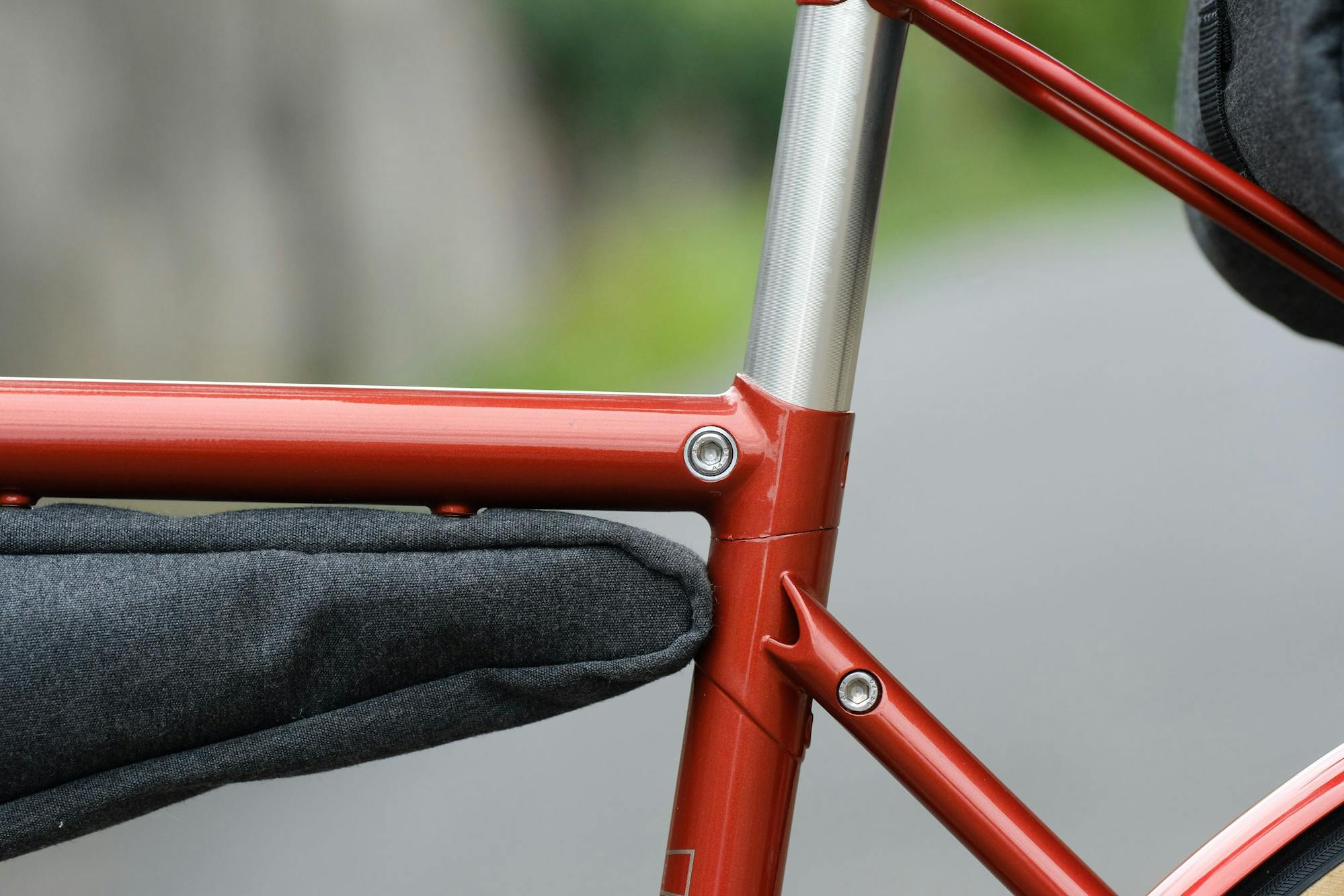
La lecture du courrier de Mr Réveur révéla un point important : ce vélo devait être démontable. Nous avions déjà proposé en 2017 une machine de ce type. Le concept mêlant système Break-away inventé par Ritchey et coupleur S&S possédait de nombreux avantages, mais aussi l’inconvénient principal de devoir transporter une clé spécifique. Nous fûmes rapidement d’accord pour repartir de cette base, tout en faisant en sorte que le vélo soit entièrement démontable à l’aide d’une clé Allen de 5mm. Pour obtenir ce résultat, nous avons conçu notre propre système de coupleurs en CAO. La fabrication a ensuite été confiée à une entreprise locale, Add-Up.
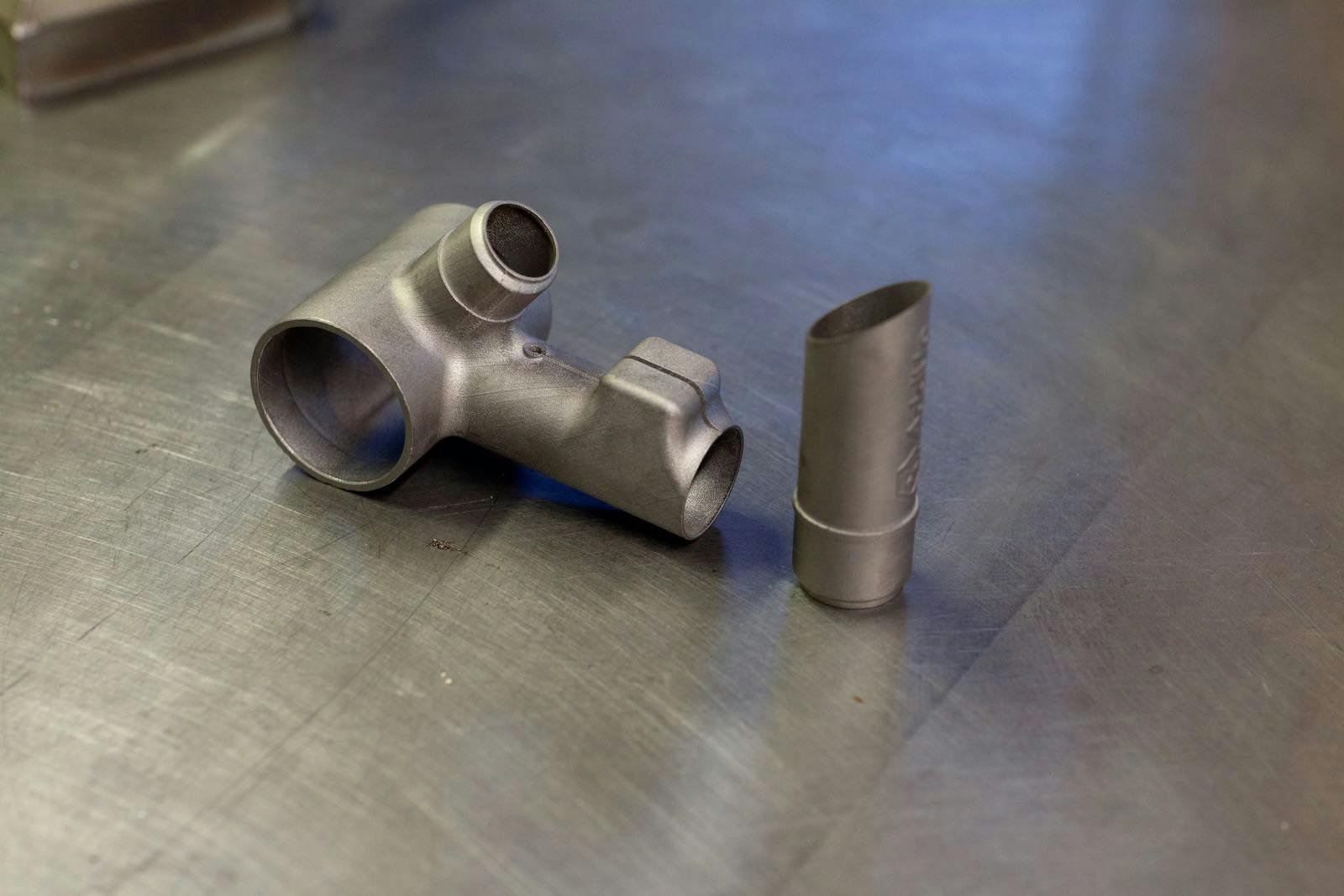
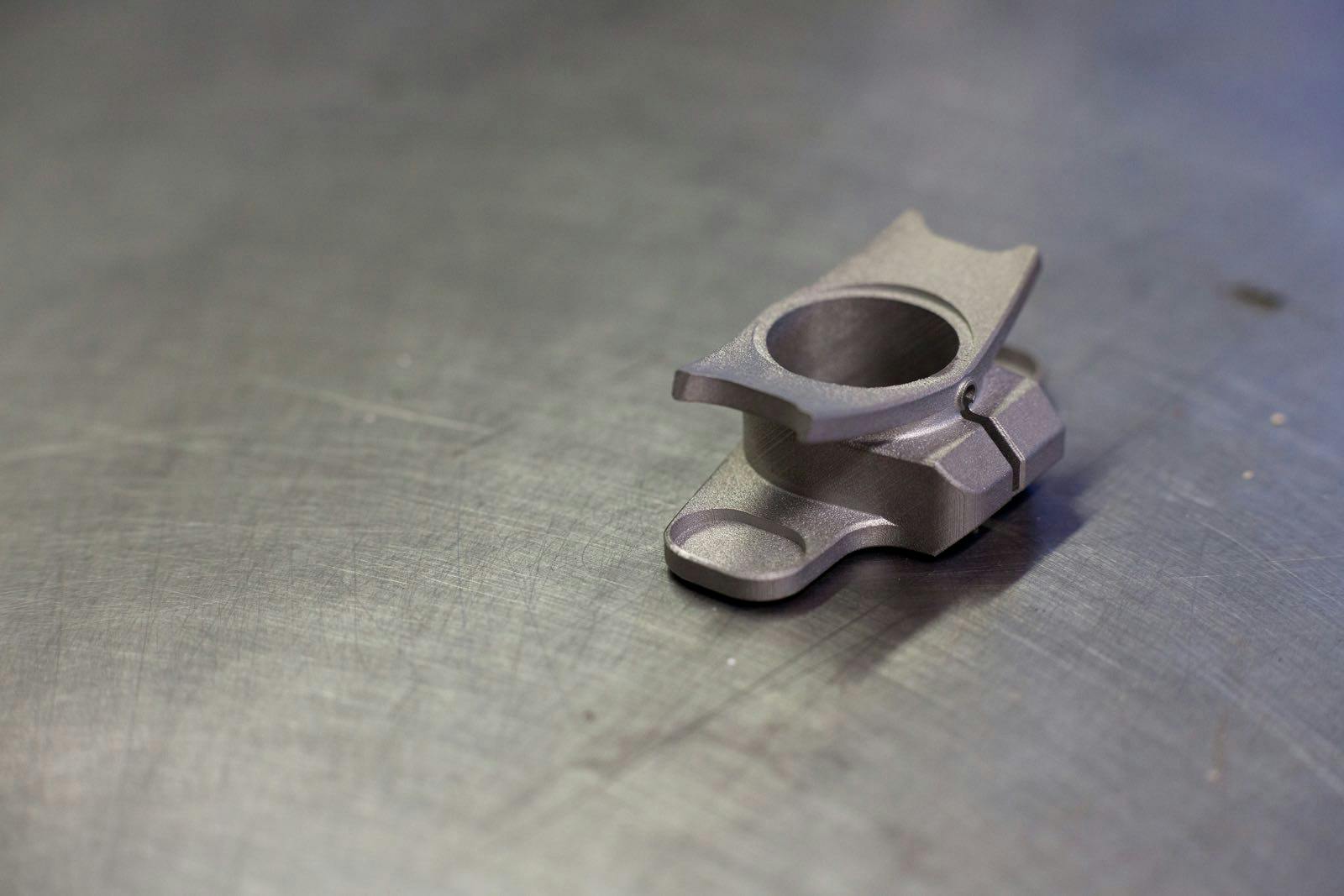
Add-Up, filiale de Michelin, est spécialisée dans la fabrication additive. Procédé récent et innovant, la fabrication additive peut être assimilée à de l’impression 3D mais ici, la technologie réalise des micro-soudures de poussière de métal de façon à monter une pièce couche par couche. Pionnier et leader du marché, Add-Up permet d'obtenir la fabrication de pièces uniques extrêmement résistantes, aux caractéristiques mécaniques supérieures aux pièces obtenues par moulage (comme les pièces de raccords de cadres). Nous avons donc conçu cinq pièces qui furent donc fabriquées à Clermont-Ferrand en acier Maraging (alliage utilisé entre autres pour fabriquer les tubes inox 953 chez Reynolds). Ces pièces remplacent un système de coupleurs ou de break-away, tout en ayant l’intérêt de la fabrication locale. L'usine Add-Up se situe effectivement à quelques kilomètres seulement de nos ateliers.
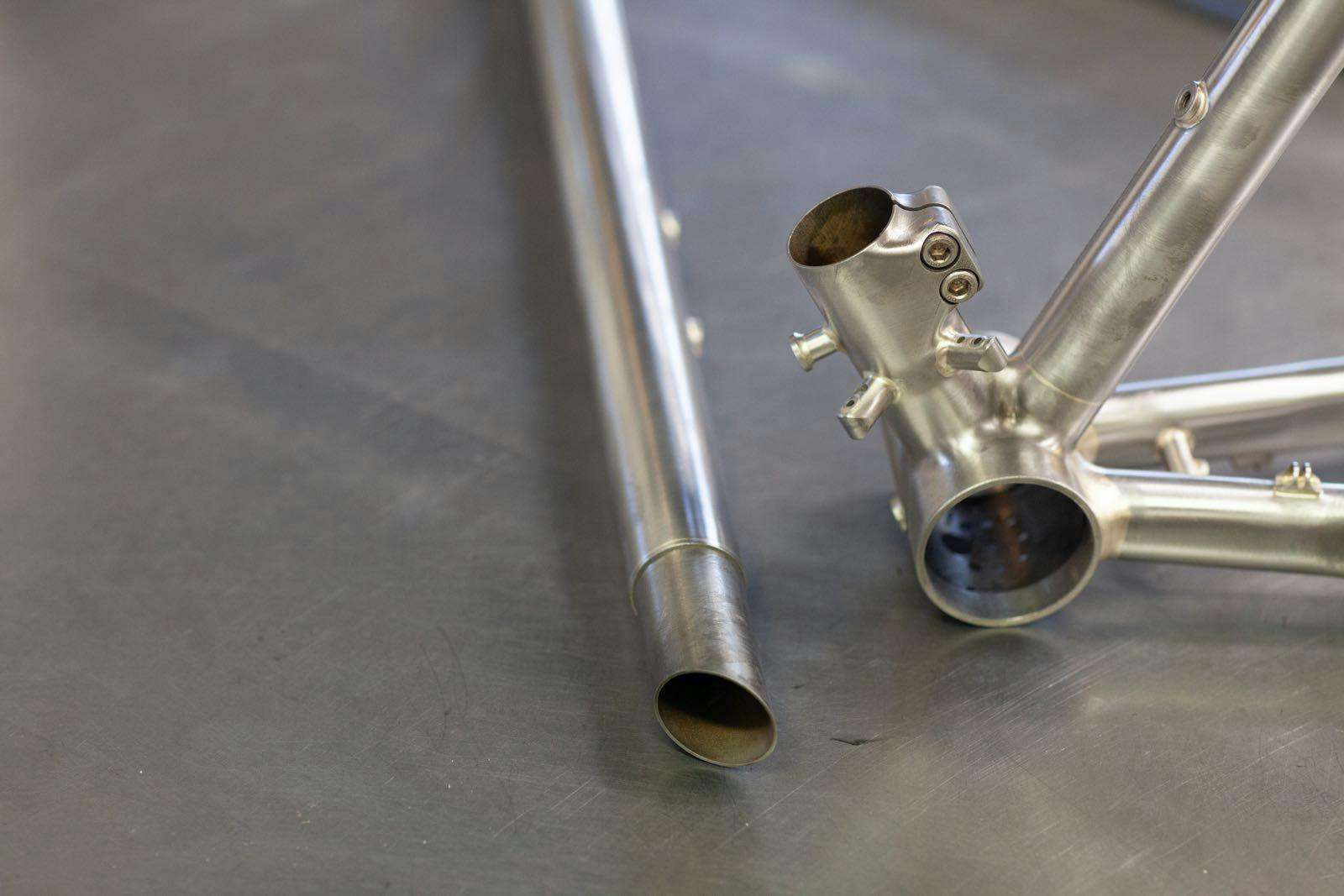
Fiers de notre savoir-faire, nous avons ensuite réalisé le cadre de façon totalement traditionnelle, avec gruges et soudures polies à la main. L'ensemble des tubes du cadre et de la fourche provient de chez nos amis italiens : Columbus. Olivier s'est chargé de la fabrication du cadre, tandis que Luka s'est penché sur l'énorme problématique du bloc fourche.
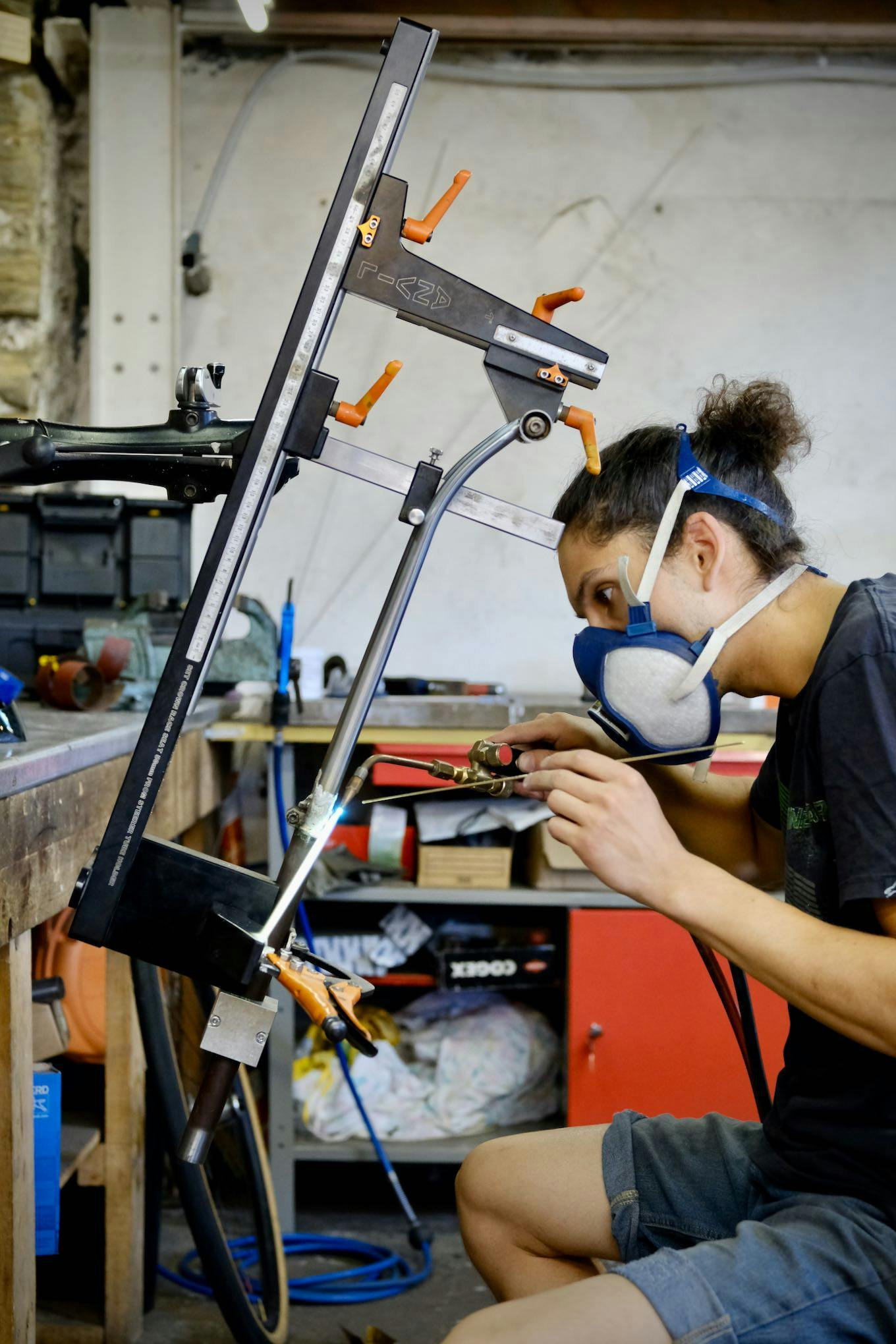
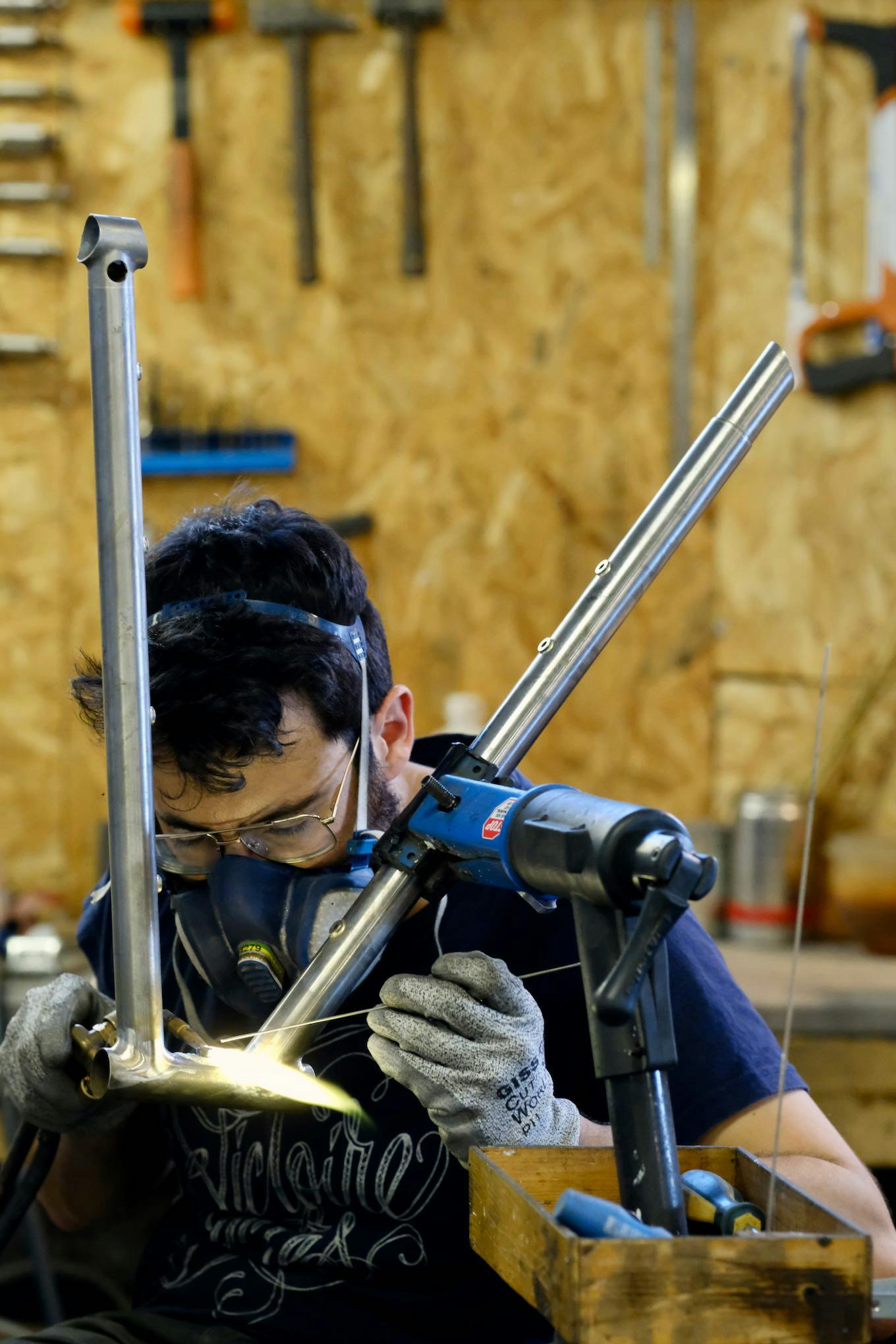
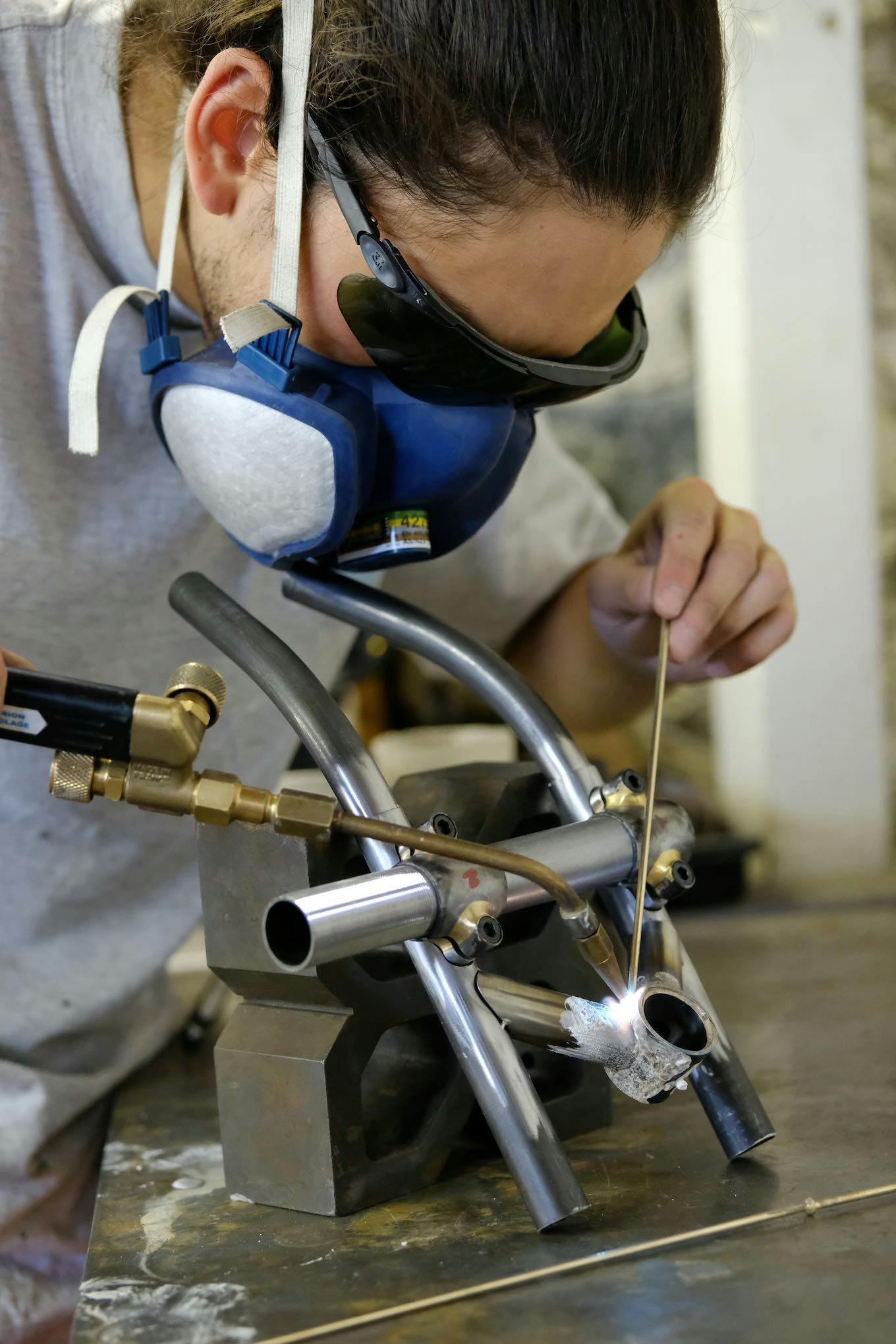

Le deuxième point concernait les problèmes d’engourdissement des mains suite aux 90h de rang à tenir le guidon. La solution classique est d’utiliser des prolongateurs de triathlon, rehaussés pour obtenir une position confortable, mais cette possibilité à l’inconvénient d’être peu esthétique et de rajouter du poids à l’ensemble du vélo. Notre réflexion part d’un constat simple : sur un vélo de longue distance moderne avec prolongateurs, l’avant est généralement très chargé visuellement, avec une multitude de tubes et des sacoches. Nous avons donc essayé de diminuer le nombre des tubes en leur attribuant un maximum de fonctions, selon le principe "less is more", cher à Ludwig Mies Van Der Rohe.
Le résultat est une pièce 100% unique, possédant à la fois les fonctions de fourche, potence, prolongateur et porte-bagage.
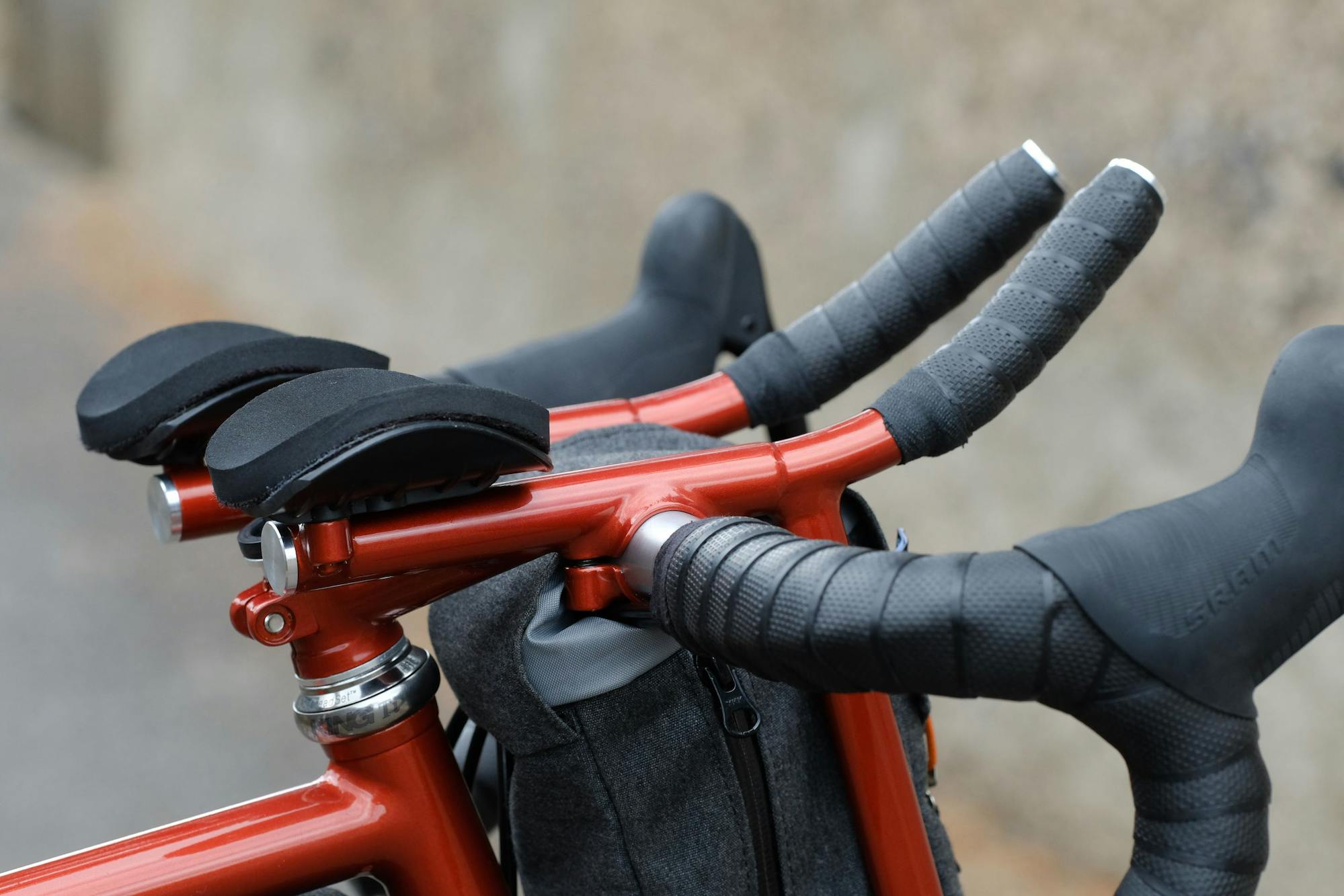
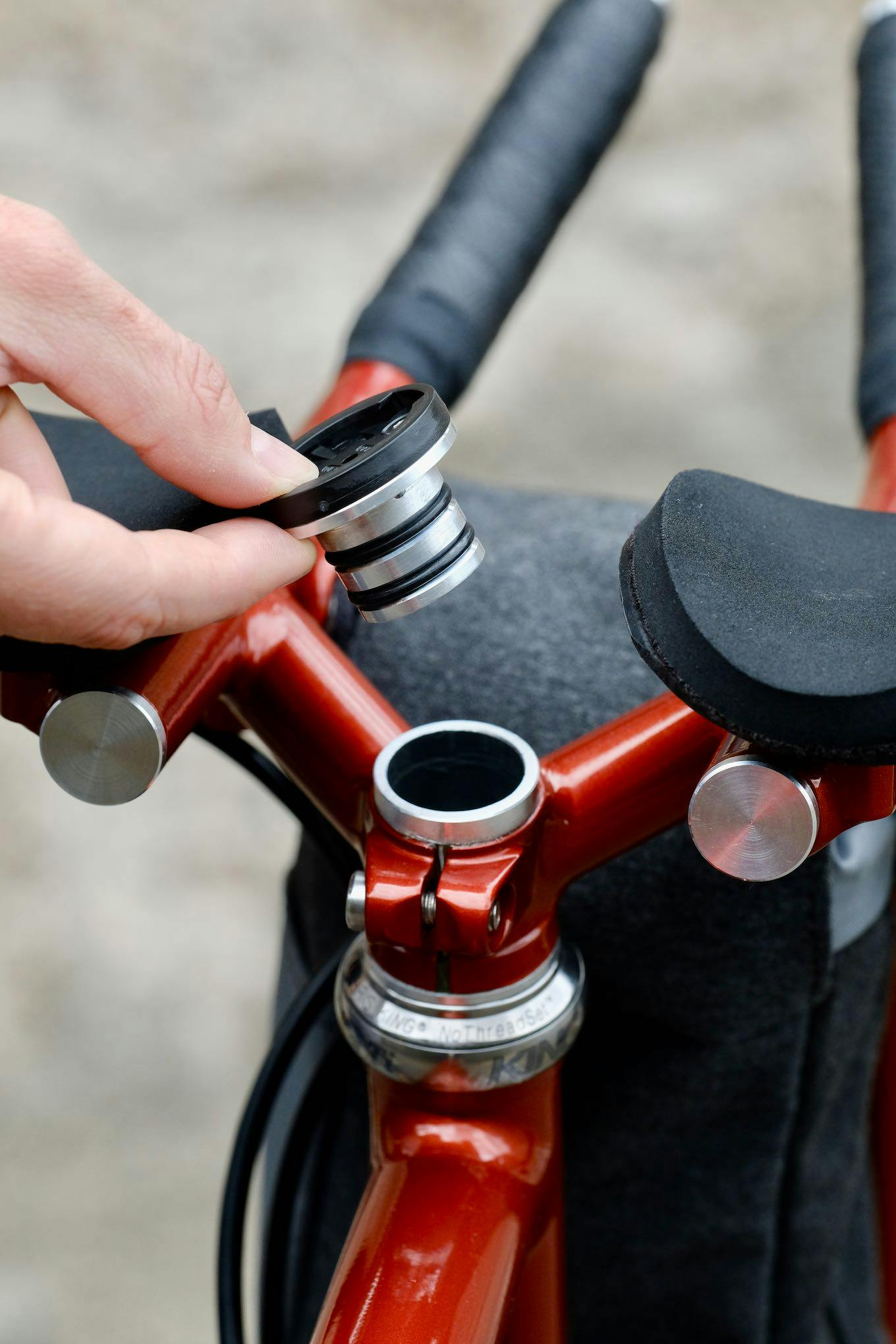
Nous nous sommes également imposés une contrainte pour cette année : réduire l'utilisation de pièces plastiques au strict minimum, et bannir complètement le carbone. Notre projet est ainsi constitué de matériaux recyclables, et nous avons privilégié les pièces robustes et faciles à réparer. Pour gagner du poids, nous avons conçu et fabriqué un maximum de composants, comme le support de GPS intégré au capot de potence, et tout ce qui ne pouvait être fabriqué à l'atelier a été modifié dans la mesure du possible.
La fabrication du cadre pour le Concours de Machines 2019 s'est étalée sur deux semaines et aura nécessité environ 50 heures de travail à deux cadreurs. Malgré la présence de pièces en fabrication additive, il a fallu réaliser de façon traditionnelle de nombreuses petites pièces et détails. Le cadre, réalisé en tubes Columbus Life, ne pèse pas plus lourd qu'un cadre classique, malgré le système de coupleurs maison. Toutes les petites pièces brasées sont réalisées en inox, de façon à supprimer toute corrosion possible. Une fois n'est pas coutume, la douille de direction est au standard 1'', malgré le système de freinage à disque. Cette originalité permet de gagner un poids conséquent sur l'avant du vélo est ce gain n'est possible que grace au design particulier de la fourche.
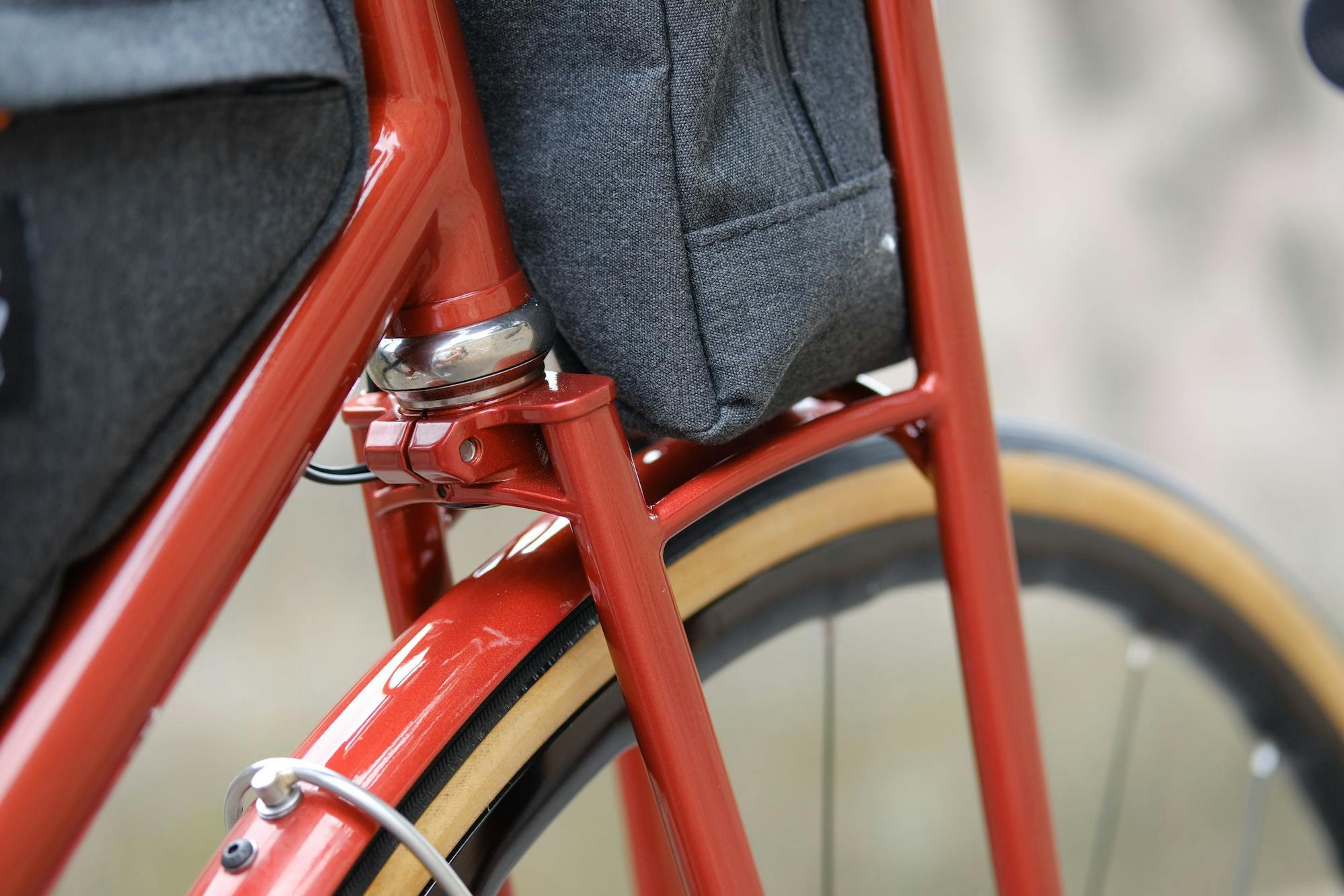
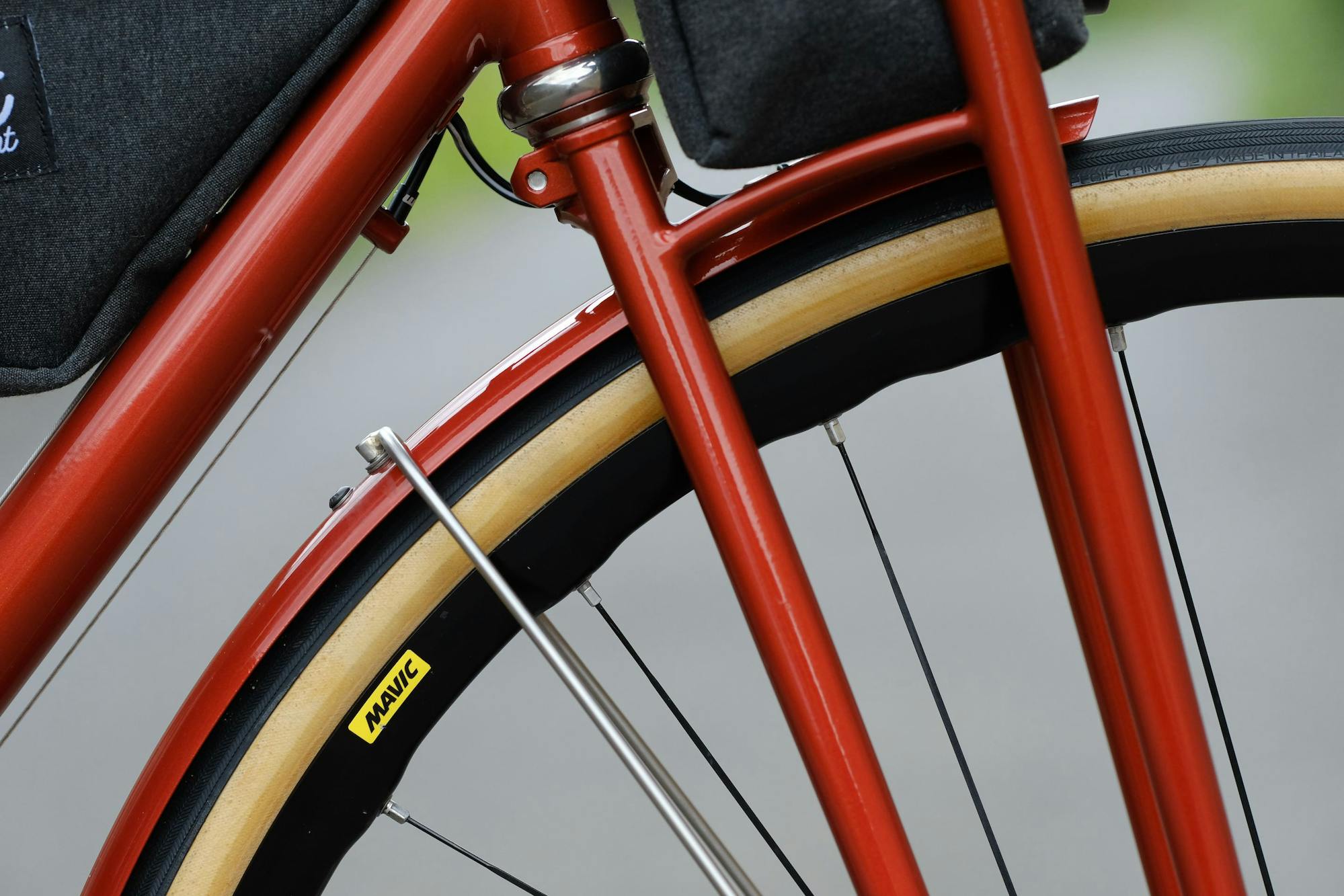
La fourche aura pris presque autant de temps que le cadre en fabrication. Ce ne sont pas moins de 45 heures de travail qui auront été nécessaires pour fabriquer cette ensemble regroupant de multiples fonctions. Le principal concept de cet objet aura été de condenser en une seule pièce la fourche, la potence, les prolongateurs et le porte-bagage. Cette technique d'intégration a permis d'économiser du poids, tout en restant sur une structure réalisée 100% en acier Columbus à l'atelier.
Nous avons pu ainsi gagner 400 grammes avec notre bloc fourche intégré, par rapport à un ensemble fourche carbone, porte-paquet, potence et prolongateurs aluminium, tout en épurant les lignes du vélo.